Optimise your ERP projects with leading SAP implementation solutions
Context
In today’s reapidly evolving business world, data is at the heart of your strategy, and new technologies are transforming the market at an unprecedented rate.
The rapid pace of digital transformation and the phasing out of legacy systems like SAP ECC are pushing Chief Information Officers (CIOs) to upgrade to cloud-based ERP systems, enhancing operational efficiency and driving business growth.
Challenge
Revitalize your information management system and IT infrastructure to stay agile and competitive in a global market.
To manage your application ecosystem with agility, you must navigate the complexities of cloud migration and address the real challenges of its adoption. Though challenging, integrating Generative AI with ERP systems is essential for maintaining a competitive edge in the long term.
Leverage the power of our ERP solutions to transform your business
VISEO is the leading SAP implementation provider with proven expertise in managing complex projects, from migration to implementation and optimisation of SAP solutions.
Transitioning to ERP demands a unique blend of technical, methodological and functional skills which can be challenging to find in a single provider. While upgrading an ERP system is crucial, it also requires a significant investment. From design thinking to integrated solutions support and third-party applications maintenance (TPM), VISEO has established itself as a trusted partner with expertise in large-scale, global rollouts of ERP solutions.
Our experts deliver a tailor-made service no matter your industry.
Our holistic approach to digital transformation allows us to view the big picture for each project. More than just an SAP implementation provider, we support you across the entire value chain—finance, customer insights, data management, application design and supply chain optimisation connecting complex, functional and modern application ecosystems together.
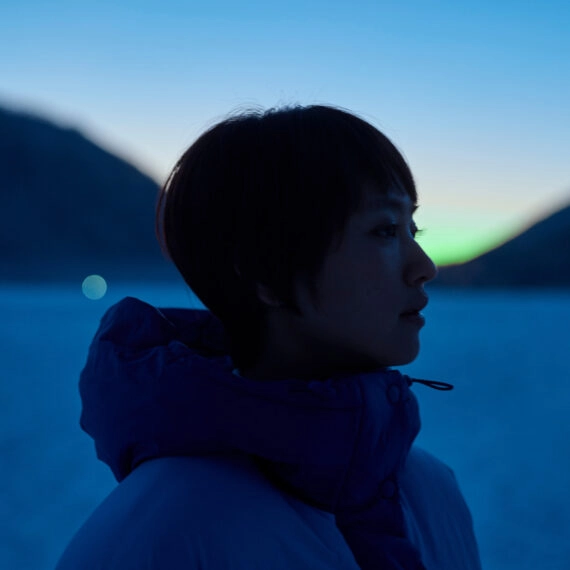
-
SAP Retail Fashion by VISEO is a comprehensive, integrated ERP solution designed to help fashion companies manage all their flows, from production to sales. It empowers businesses to enhance customer understanding and manage global inventories and their supply chain. This solution also ensures a seamless and unified customer experience, connecting the physical store with the digital universe.
-
The RISE with SAP offering is a comprehensive ERP solution designed to help food manufacturers manage accounting, purchasing, production, sales and supply chain processes, leveraging specific features such as MRP and traceability. It integrates business processes from Lead-to-Cash to Design-to-Operate, all while optimising total cost of ownership and simplifying maintenance. Tailored to the specific needs of the food-processing sector, this solution can also help industry players to manage complex contracts and products with weight variability.
-
Move to the Cloud with S/4HANA by VISEO offers organisations a strategic assessment to prepare their transition to S/4HANA. The offering includes detailed planning, change management support and technical architecture design, with a view to optimising migration and ensuring effective adoption before 2030. This approach encompasses the organisation of workshops, project assurance and governance, as well as training and communication strategies, all to ensure maximised benefits and risk mitigation. Our ultimate goal? Optimising resources and efforts for a seamless cloud migration journey.
-
We guide our clients through five crucial steps: audit and preliminary analysis, a detailed pre-study, including the choice of technical solutions and process optimisation, the provision of a Proof of Concept for Brownfield scenarios, personalised support during conversions and migrations, and activation of tailored complementary services. This offering ensures a successful transition to S/4HANA in alignment with each client’s business goals, addressing all possible scenarios with a customised approach for each configuration — whether cloud-hosted or not.
-
The SAP FSM offering by VISEO combines responsiveness and efficiency to optimise resource utilisation. Using the latest technologies such as mobile tools, AI and machine learning, this solution encompasses all aspects of service, from initial contact to final report, with a view to increasing customer satisfaction and revenue. It simplifies access to information for customers and automates planning for team leaders, providing an accurate view of available technicians and their locations to ensure efficient service management and delivery.
-
SAP IBP offering by VISEO is an advanced solution for supply chain management and optimisation. It improves forecasting and collaboration and creates supply plans to enhance service while reducing inventory. We leverage its supply chain experience to anticipate needs through efficient capacity management and plan simulation. It combines expertise in IBP and ERP to optimise end-to-end processes and integrate data models, with a view to improving supply chain performance and information systems.
-
We offer comprehensive support for your SAP systems, ensuring corrective, preventive, and evolutionary maintenance. Our dedicated team, available 24/7, provides support in all functions (FICO, MM/SD, PP, WM, CX, etc.) and technical infrastructure. The service is structured by a catalog defining a base and Time & Material for additional services. With more than 22 years of SAP expertise, we are PCoE-certified and have a large team of specialists with experience across all sectors. Our managed services are provided by qualified RISE teams, with nearshore pooling options through our centres of excellence in Casablanca and Cebu.
-
VISEO leverages SAP BTP to create personalised experiences, accelerate the development of applications, analytics and integrations, and implement strategic, innovative solutions with confidence. We take advantage of SAP BTP tools to seamlessly connect, develop and enhance business-critical processes. Companies use this platform to automate tasks, create flexible workflows and customise interfaces with low-code solutions. This facilitates collaboration across various functions such as finance and sales, seamless integration with SAP and third-party applications, and the sharing of real-time insights.
-
VISEO integrates global data management solutions to adapt to the evolving role of chief financial officers. In collaboration with chief information officers, we ensure the successful implementation of SAP S/4HANA Cloud in 14 weeks, using SAP FC and SAP Group Reporting for reporting and consolidation and SAP BPC and SAC Planning for EPM. VISEO manages international projects supported by RISE teams, accelerators, methodological kits, and a dedicated university. They also provide 24/7 support and AMS from Casablanca and Cebu.
-
XPERT Sustainability by VISEO is designed to help companies comply with new non-financial reporting requirements (i.e. CSRD, EU Taxonomy, CSDDD). This modular and customisable end-to-end solution is integrated with SAP RISE and applies the SAP Activate methodology. VISEO provides a team of experts, technological accelerators (Datasphere, Cloud Platform Integration/API), and prototype SAP Sustainability environments. Additionally to leveraging SAP tools, XPERT Sustainability is designed to help organizations understand the impact of materials across the value chain and design sustainable and regulatory-compliant products that meet ecodesign requirements.